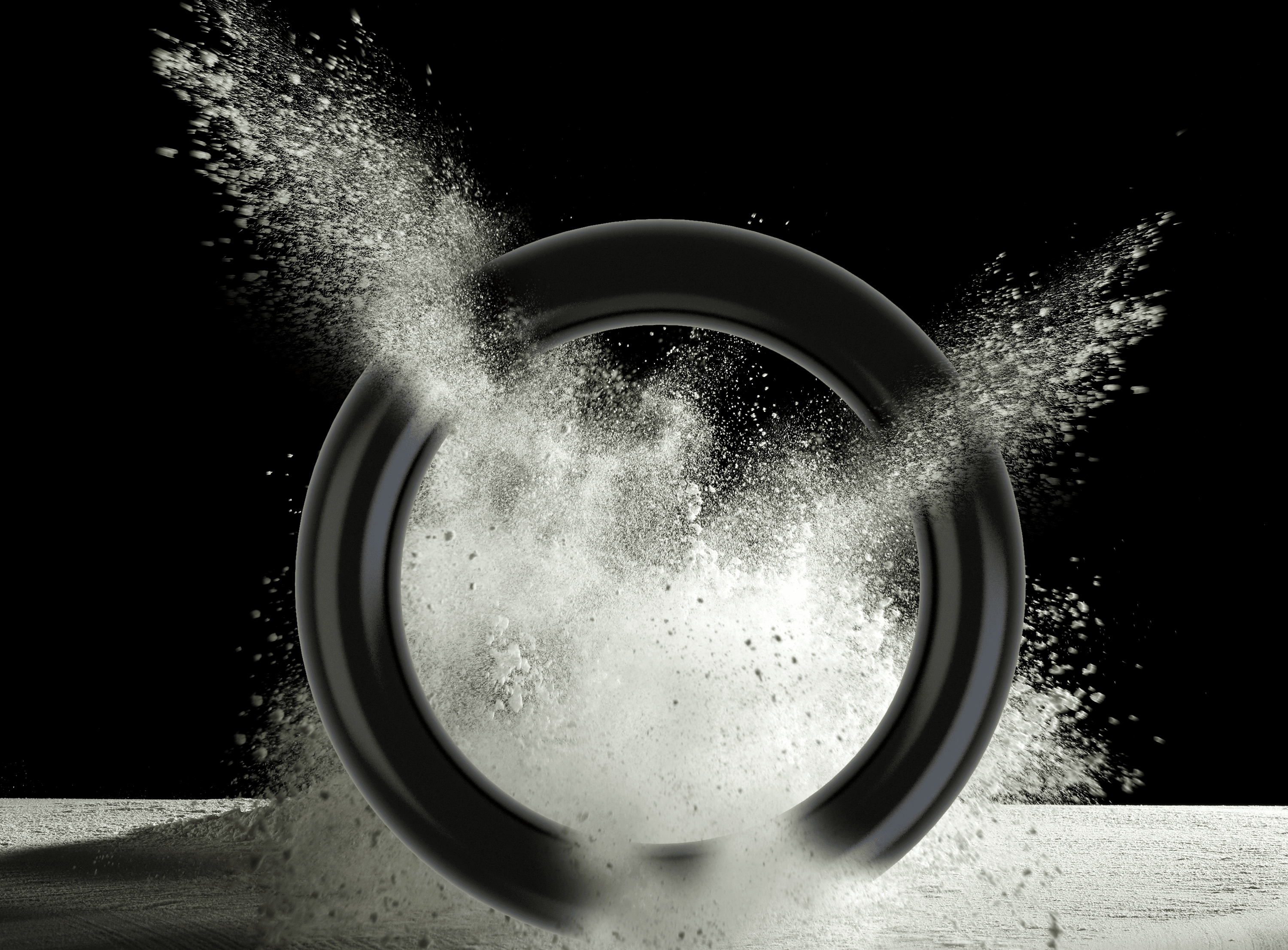
Are you familiar with the special types of treatment applicable to O-rings?
Treatment designed to improve the performance of O-rings
Standard elastomer O-rings sometimes need to undergo special surface treatment. This will enhance the performance of the equipment and levels of productivity in the assembly and mounting processes in which these seals are used.
We at JIOrings treat the surface of O-rings using special cleaning, immersion or coating processes, with the aim of reducing friction and adhesion in order to achieve a permanent lubricating effect and to facilitate the installation of the seals.
This treatment is usually carried out on large quantities or batches, however, if you have any such needs, we recommend you contact us to enable us to analyse your request and propose the appropriate solution. We provide the following different types of treatment and surface coatings:
- PTFE
- Coloured PTFE
- Silicone
- Talc
- Micro Talc
- Molykote
- Graphite
- Chloride
- Rough
*Requesting and downloading the technical data sheets for each type of treatment is subject to the purchase of seals subjected to any of the aforementioned coatings.
PTFE
PTFE (polytetrafluoroethylene) coating, also known as TEFLON® (the registered trademark of Chemours), is a fluoropolymer-based coating designed to provide excellent anti-adherence to the seals.
PTFE is a material that is suitable for contact with food (FDA), and as such is used in many industrial sectors such as food, beverages, chemicals, textiles… The process for coating seals with PTFE Teflon® consists of four different stages:
- Degreasing – Consists of the removal of any organic or inorganic residue on the parts. The seals to be treated need to be degreased to do this.
- Sandblasting – The preparation of the surface to be coated in order to guarantee the maximum adherence of Teflon® by sandblasting with aluminum oxide.
- Application – This is conducted using liquid, electrostatic, HVLP spray guns or powder guns. The process can consist of several layers of product, depending on the purpose of the coating.
- Curing – The coating needs to be polymerised to ensure Teflon® retains all its properties. This involves keeping the seals at a temperature of 360 ºC for 10 minutes.
SILICONE
A silicone coating provides seals with greater anti-adherence, impermeability and mechanical resistance. In addition, silicone seals have better sealing and thermal insulation. A silicone seal has the following advantages:
- Greater thermal resistance.
- Good flammability properties.
- Excellent impermeability (even in hostile conditions: weather, water, steam, smoke and combustion gases).
- Excellent flexibility.
- Easy to clean.
- Greater durability.
MOLYCOTE
Molykote is the trade name for special Dow Corning lubricants. This lubricant is designed to deal with industrial lubrication issues and to reduce friction and wear.
Treating O-rings with Molykote, which features molybdenum disulfide (MoS2) in the lubricant, gives rise to an end product capable of withstanding high loads, high and low working temperatures, dirt and dust, aggressive chemical environments and extreme speeds.
The MoS2 is placed in the elastomer in the form of a dry lubricating film by deposition on the sealing surface. This produces a mechanical interlock, which reduces friction and wear caused by dynamic stress in the long term. The main advantages of this type of treatment are:
- It improves separation in automatic assembly.
- It reduces friction and dynamic stress.
- It controls contamination.
- It provides protection against corrosion.
- It dissipates heat.
- It transmits power.
- The process is suitable for all types of elastomers.
When used on O-rings, this static lubricant enables them to be used in advanced applications that require high electrical conduction, heat transfer, vacuum sealing and/or shear stability.
TALC
It is often necessary to improve the friction coefficient of O-rings, as they normally have rough and sticky surfaces. In these cases, surface treatments such as talc can be used. This method reduces friction, both to facilitate assembly and to prolong service life.
Treatment with talc consists of applying a powder coating to seals in a drum. No crosslinking with the elastomer surface occurs in this process.
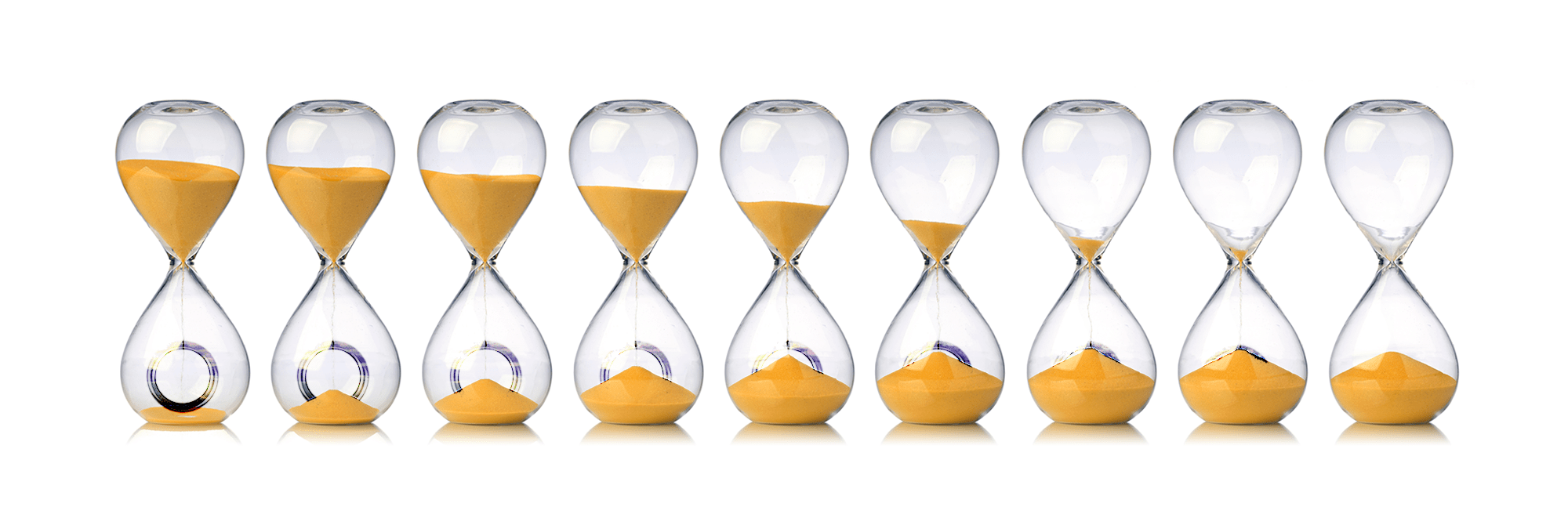
What is the service life of an O-ring?
Gaskets also age
We need to differentiate between the time for which a gasket can or should remain in storage and its time of use, or in other words, its passive shelf life and active service life.
The service life of O-rings is governed by international aerospace regulation SAE AS5316, which defines all storage and service life conditions for elastomer products:
Material | Service life |
FKM | Unlimited |
FVMQ | Unlimited |
HNBR | 15 years |
NBR | 15 years |
FFKM | Unlimited |
PTFE | Unlimited |
VMQ | Unlimited |
We should not forget, however, that the information in this table is not binding. This information should be used simply as a basis on which to establish the requirements for the service life of gaskets, which will depend on the conditions to which they are subjected.
To ensure the longest possible service life of gaskets without them losing any performance with regard to what they are intended for (sealing properties), they must be stored properly, installed carefully and the conditions to which they are exposed must be known in order to conduct replacement or maintenance work when required.
The efficacy and duration of the sealing effect of O-rings are linked to the maintenance of their chemical and physical characteristics.
Tips for proper storage
Following a few basic storage tips will enable you to ensure your gaskets have a long service life.
- They should be stored at a temperature of between 15 °C and 38 °C.
- Relative humidity should be less than 75%.
- Gaskets should not be exposed to direct sunlight.
- They should not be exposed to sources of ionising radiation.
- They must not feature any kind of deformation and they must be tension-free.
Tips for installation
If you assemble a gasket incorrectly, this could cause superficial scratches that will undermine its sealing capacity and cause the mix to age prematurely.
The replacement of any gasket (in poor condition) entails shutting down the facility and often complex maintenance activity that needs to be scheduled in order to mitigate the economic impact thereof.
The integrity of a gasket may be compromised in the assembly or installation phase, hence the following should be taken into account:
- Avoid superficial damage: for which we recommend the use of lubricants or stretching the ring in order to widen the inner diameter.
- Avoid twisting the O-ring section: for which we recommend the use of Quad-Rings and their four support points, which are ideal for hydraulic, pneumatic and mechanical applications.
Depending on whether the installation is radial or axial, we will select a gasket with an inner diameter equal to or less than the diameter of the part to be sealed.
Check out our installation tips.
Once gaskets are in place, it is almost impossible to define their service life, as this will depend on all the factors involved: time of use, friction, temperature, fluids…, however proper installation and monitoring while they are active are important.
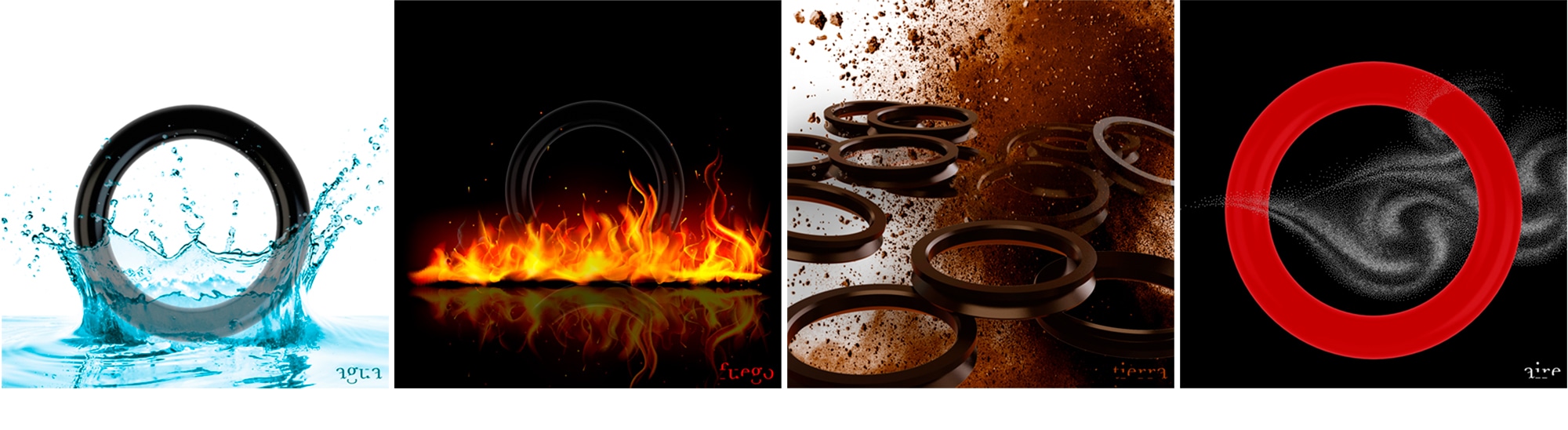
O-Rings for all four elements
Discover some applications of the sealing gaskets
Our seals are prepared to give their best in the 4 elements of nature (water, fire, earth and air), their main function being to ensure fluid tightness between the union of two surfaces, for example, in hydraulic cylinders and pneumatic cylinders. But the reality is that we can find them in an infinite number of “scenarios” related to the 4 elements:
W A T E R
- O-rings for drinking water with specific approvals (ACS CLP, 3A, EN681, KTW-UBA, KIWA, NSF61, WRAS, W270, W534)
- O-rings for various water treatments such as filtration, purification, desalination, irrigation, pumping…
- O-rings for oceanographic buoys.
- O-rings (green FPM) for marine engines.
- O-rings for diving equipment (TW-UBA, KIWA, NSF61, WRAS, W270, W534).
F I R E
- Seals for high temperatures and flame retardant seals with specific approvals (UL)
- O-rings for fire extinguisher pressure gauges.
E A R T H
- O-rings and X-Rings for agricultural machinery that prevent dirt from entering the shafts.
- ME2 scrapers for public works machinery.
- O-rings for fastening mining masonry.
A I R
- Special EPDM O-rings for oxygen for ventilators in hospitals.
- Gaskets to create a seal on a surface that carries gas with specific approvals (EN549/EN682).
- O-rings for compressed air rifles.
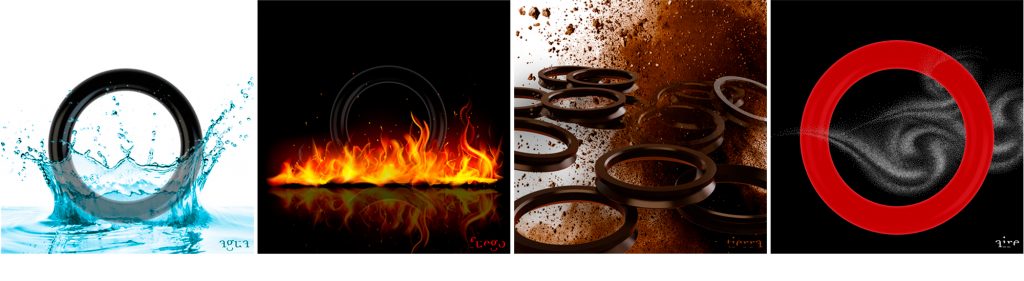
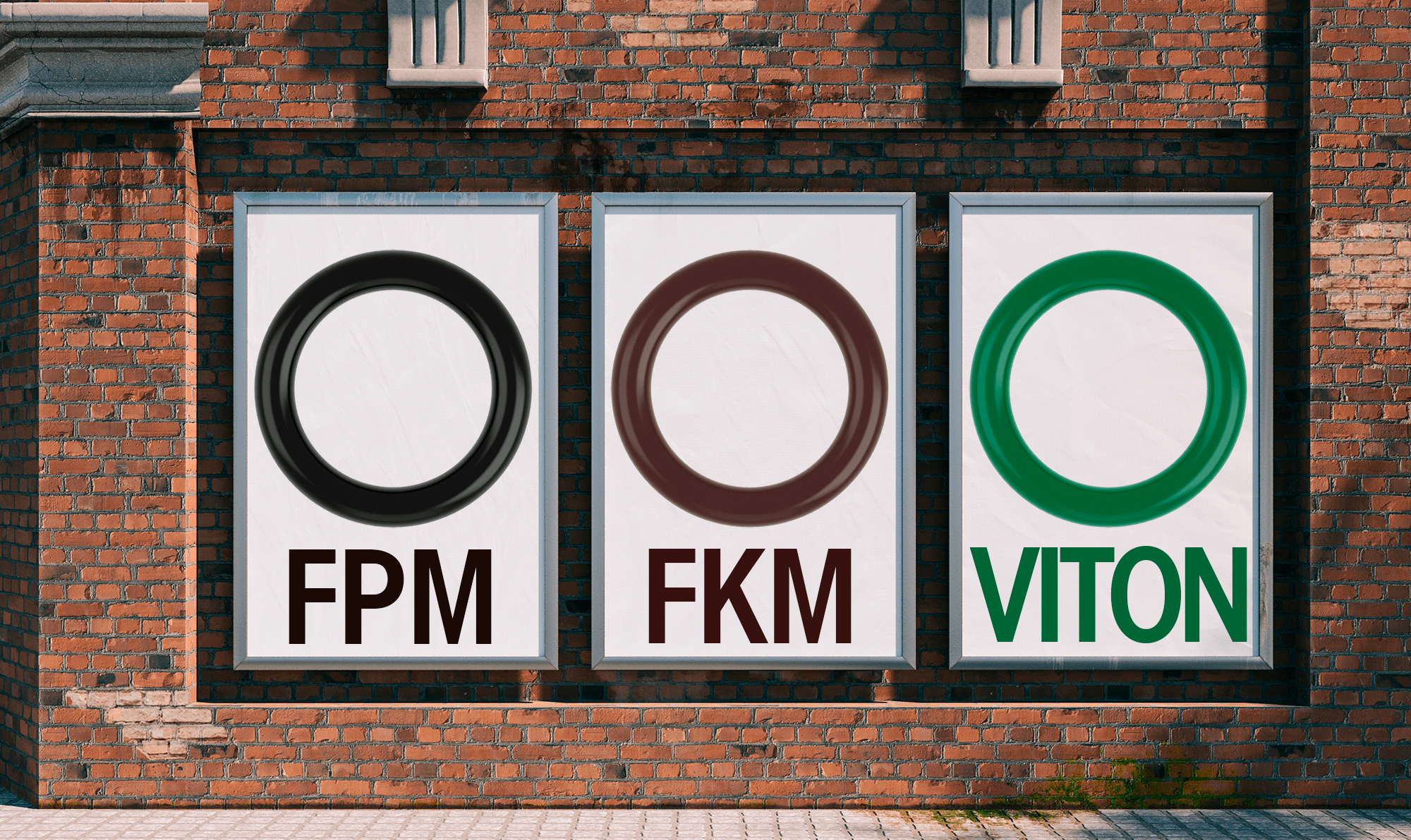
FKM/FPM/Viton®, three names for the same rubber
Do you know what Viton® is?
Viton® is a trademark of a synthetic rubber and fluoropolymer elastomer commonly used in the manufacture of O-Rings. The name is a trademark registered by The Chemours Company and its international abbreviation is FPM (DIN/ISO denomination) or FKM (ASTM). It is also known as Fluoro-Elastomer or by its trade name, Viton.
The Viton® brand is by far the most recognised FPM/FKM brand worldwide, to such an extent that, in the industrial world, the word has undergone a lexicalisation process. In other words, like the word Kleenex® designates a tissue, the word Viton® is used to refer to gaskets manufactured in FPM regardless of their raw material. The truth is that, since its invention by DuPont™ (now The Chemours Company), many other chemical companies have developed their own FKM. We can cite Dyneon®, DaiEl ®, Fluorel®, Noxtite® and Tecnoflon®, among others.
DuPont, an American multinational company, is one of the largest chemical companies in the world. As well as having developed Viton, it is also the creator of other well-known materials such as Neoprene®, Nylon®, Lycra®, Plexiglass®, Teflon®, among others. Because it always trademarks its progress, many of its products are even more famous than the company itself.
Why do our customers choose the Viton® O-rings?
Basically, because their thermal resistance is the best, no other elastomer can compare.
Viton® is a hexafluoropropylene thermopolymer, with vinylidene fluoride, tetrafluoroethylene and methylvinyl etherperfluoro. On the one hand, the energy of the carbon-fluorine bond is much greater than that of the carbon-hydrogen bond and also greater than that of the carbon-chlorine bond. On the other hand, the much larger fluorine atoms exert a shielding effect, which protects the main carbon chain. Hence its thermal resistance.
The resistance to continuous temperature is +205 ºC without losing its mechanical properties. In intermittent, it can reach up to 220°C. Some “improved” compounds like our “OZM410-121294” blend resists temperatures of up to +250ºC.
Stock of O-rings in Viton®
At JIOrings, we have an extensive stock of Viton gaskets and the possibility to manufacture in this material or schedule their manufacture. As well as O-Rings, we also have quad-rings, V-Rings, cord-rings and seals (in high demand) in Viton.
Did you know that...?
The surname “Vitón” is quite common in Spain and comes from the Latin “vita”. Apparently, it appears 234 times as a first surname and 206 times as a second surname. Nobody has it as both surnames. It is also a surname that appears in the Sephardic community of Morocco.
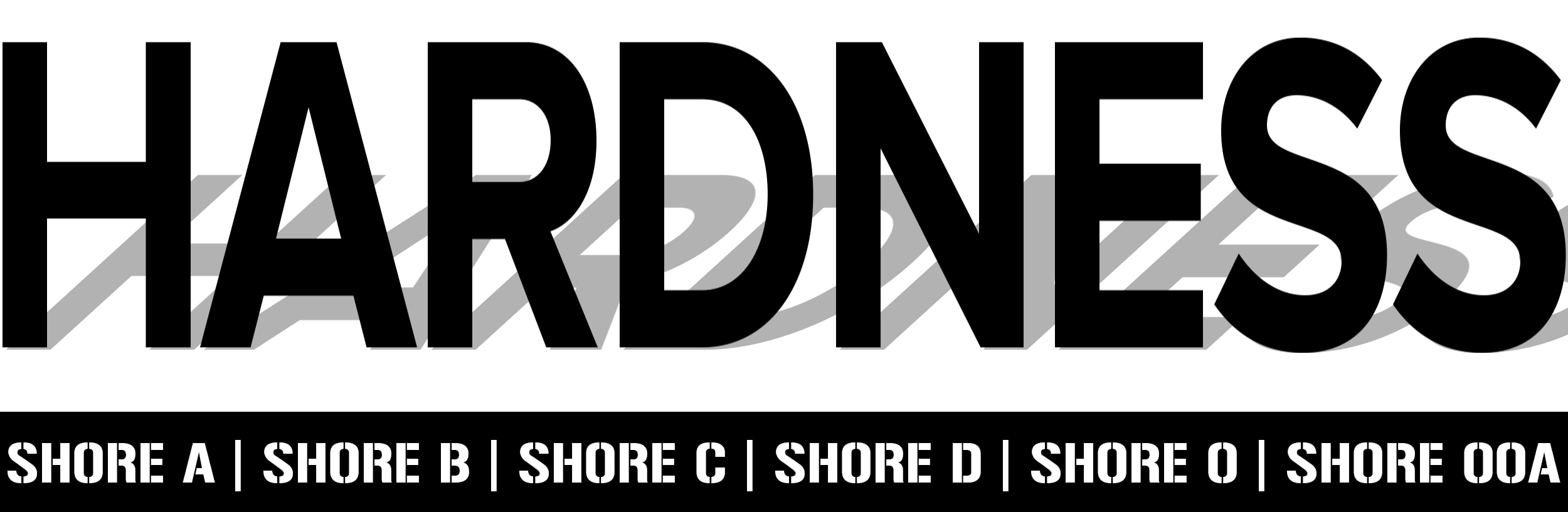
What is Shore A Hardness?
Because hardness matters too...
This is one of the most used scales for measuring the hardness of elastomers. Although it is not the only one, apart from scale A there are scales B, C, D, 0 and 00. Of these, the Shore D scale is also used to measure the hardness of harder elastomers.
The hardness of an elastomer represents its stiffness against moderate stress, such as those that it frequently subjected to in an application.
There are two methods for obtaining the hardness of O-rings and other seals:
Durometer
A durometer is an instrument with a frusto-conical tip that, on penetrating the elastomer, produces a reaction in the calibrated metal spring. When the Shore A durometer indicates readings of greater than 90°, the use of the Shore D durometer, which has a tapered tip and a stiffer spring, is recommended.
To ensure the correct use of this measurement tool, we at JIOrings recommend:
• Using the durometer on a flat, clean, polished surface.
• Measuring perpendicular to the durometer´s indenting foot.
• Repeating the test 3 times in a different place on the part/seal each time.
Due to its simplicity and convenience, the Shore hardness form of measurement is widely used as a production control. The use of IRHD hardness is recommended for the purpose of more exact classification or specification:
Macro IRHD
This durometer is designed to obtain hardness in all types of elastomers and plastics with a minimum thickness of 6 mm. The system consists of a stand with a testing table and a macro head designed to accommodate IRHD N, IRHD L, IRHD H and Shore inserts. The inserts feature 1, 2.5 and 5 mm diameter ball indenter and test loads from 2.65 to 5.70 N.
Micro IRHD
A micro durometer is used to obtain hardness in all types of elastomers and plastics with a maximum thickness of 5 mm. The system consists of a stand with a testing table and a micro head with a 0.395 mm diameter ball indenter and test loads from 8.3 mN to 153.3 mN. The measurement stroke is 0.3 mm and the range is between 30 and 100 micro IRHD.
Hardness equivalence table
Shore A | IRHD | Shore D | Shore 0 | Shore 00 |
DIN 53505 | ASTM D 1415 | DIN 53505 | ASTM D 2240 | ASTM D 2240 |
Compact and cellular elastomers | Compact elastomers | Polyurethanes, rigid PTFE, thermoplastics and very hard elastomers |
Medium density compact and cellular elastomers | Medium and low density cellular elastomers |
100 | 100 | 58 | ||
95 | 95 | 46 | ||
90 | 90 | 39 | ||
85 | 85 | 33 | ||
80 | 80 | 29 | 84 | 98 |
75 | 74 | 25 | 79 | 97 |
70 | 68 | 22 | 75 | 95 |
65 | 64 | 19 | 72 | 94 |
60 | 62 | 16 | 69 | 93 |
55 | 54 | 14 | 65 | 91 |
50 | 49 | 12 | 61 | 90 |
45 | 44 | 10 | 57 | 88 |
40 | 39 | 8 | 53 | 86 |
35 | 35 | 7 | 48 | 83 |
30 | 28 | 6 | 42 | 80 |
25 | 35 | 76 | ||
20 | 28 | 70 | ||
15 | 21 | 62 | ||
10 | 14 | 55 | ||
5 | 8 | 45 |
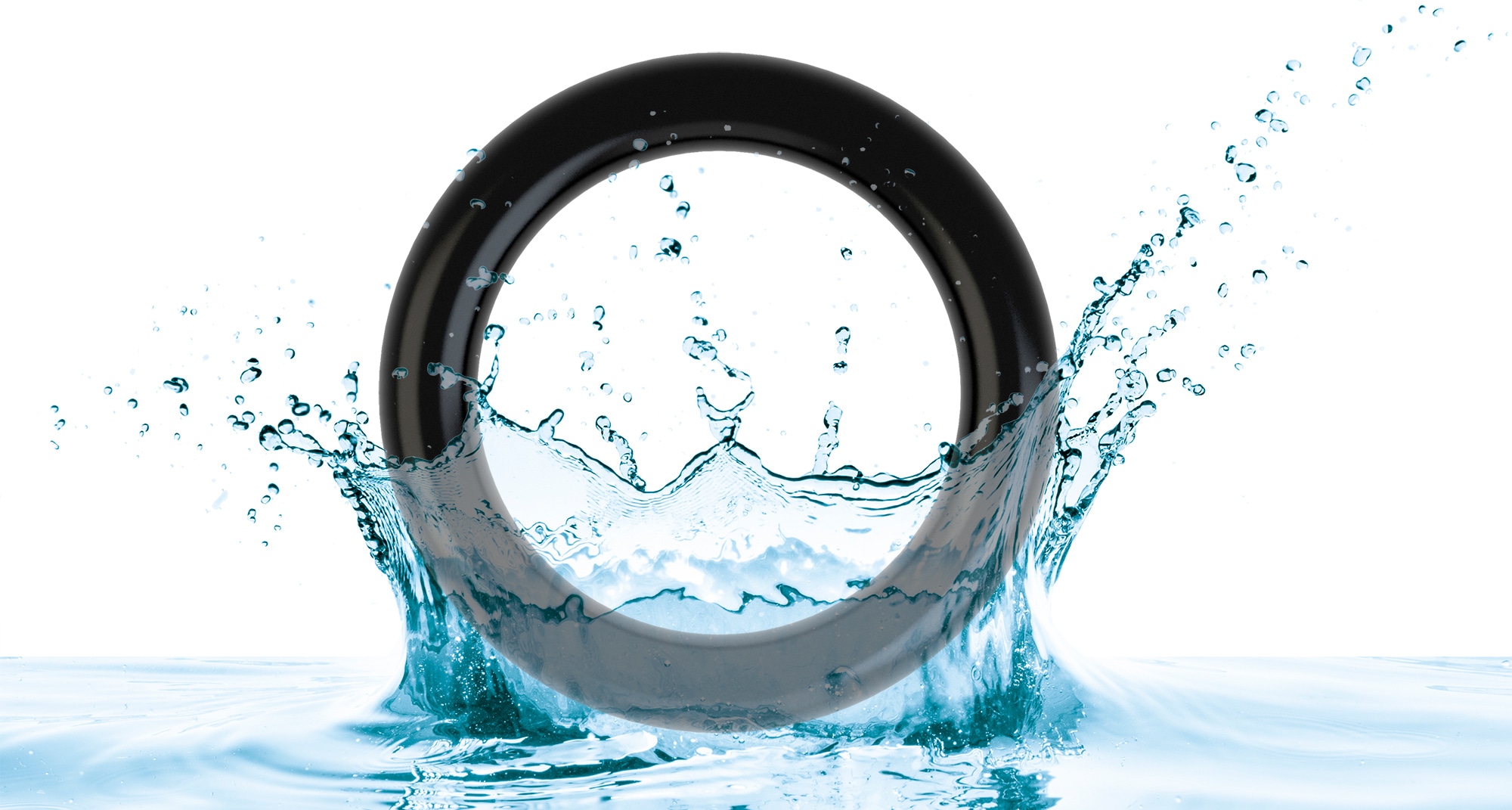
We make every drop of water count
Water-responsible O-Rings
Water is a limited asset, one of the most important resources we have and which we need to manage and take care of accordingly.
We use large amounts of water for domestic purposes every day – for drinking, showering, flushing, cooking, mopping…. Indeed, according to the INE (National Institute of Statistics), the consumption of water in Spanish homes is 132 litres per person per day.
Moreover, water is also vital for industry (as an ingredient for the product to be manufactured and as part of the production process) and for agriculture (irrigation) too.
Whatever the use, we at JIOrings help companies (desalination plants, water suppliers, drinking water treatment plants, irrigation firms…) to achieve optimum watertightness in water piping to ensure there are no leaks. The watertight properties of our O-Rings designed for water piping valves and accessories ensure that not a single drop is wasted.
To this end, we analyse each company´s needs and supply the ideal O-Ring for each use. The size, cross-section, hardness and material of the product, in addition to the required approvals, will vary in accordance with the needs of each individual customer. All our years of experience enable us to meet the needs of water suppliers through the annual programming of their most common measurements. Furthermore, to manufacture and supply special sized seals.
We also market the star mix for the sector related to the supply and treatment of water: LPM534 EDPM FDA for DRINKING WATER.
O-Rings installed in valves, pumps, piping and similar applications should be resistant to the fluid itself without the need to add any ingredient or alter the essential characteristics of the product being conveyed, such as the colour, smell or flavour.
This mix, approved by the German Environmental Agency (Umwelt Bundesamt, UBA), complies with all the hygiene and toxicology requirements established by this agency and those of European Regulation CE/1935/2004.
We at JIOrings adapt to each of our customer´s requirements and the standard in relation to O-Rings in each country. We always attach the corresponding certificate attesting to our compliance, thereby guaranteeing the suitability of our O-Rings for each specific purpose.
What about you, what seals do you need?
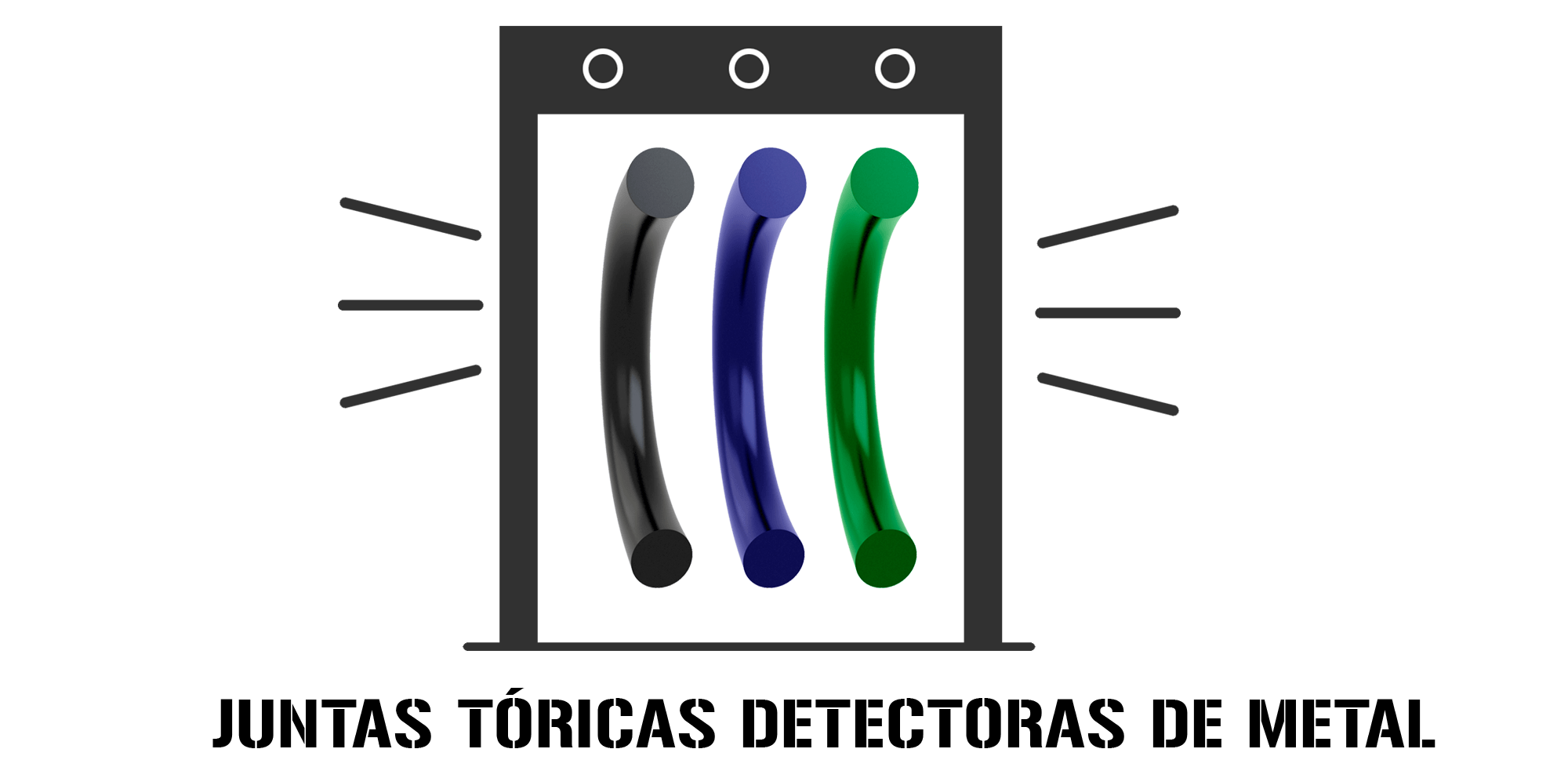
Metal detectable O-rings
¿Sabías que hay juntas tóricas capaces de detectar el metal?
El uso de las juntas tóricas en las industrias alimentarias y farmacéuticas es muy habitual. La mayoría de los equipos convencionales de detección de metales son capaces de revelar inmediatamente dicha alerta de contaminación.
A diferencia de otras industrias donde el material de la junta o su resistencia a altas temperaturas puede ser la propiedad clave a la hora de seleccionarlas, en las aplicaciones farmacéuticas y alimentarias la clave es la seguridad.
En JIOrings garantizamos la seguridad del producto y el cumplimiento de las normativas FDA, proporcionando a nuestros clientes una gama de juntas tóricas detectoras de metal (o capaces de detectar el metal), que han demostrado ser la solución más rentable y segura para garantizar su uso en aplicaciones alimentarias y farmacéuticas.
Las juntas detectoras de metal solo están a la venta bajo pedido y a partir de una cantidad mínima. Contacta con JIOrings para que podamos realizar un presupuesto a la medida de tus necesidades.
Material | Dureza | Color | Compuesto | FDA | Observaciones |
NBR | 65 | Azul | IB656457 | ||
NBR | 70 | Azul | IB706435 | ||
NBR | 70 | Blanco | IB708452 | Sí | |
NBR | 70 | Negro | IB701439 | Sí | Curado al azufre |
NBR | 75 | Verde | IB755450 | Sí | |
FPM | 75 | Azul | OZ756317 | Sí | |
FPM | 75 | Negro | OZ751277 | Sí | |
EPDM | 70 | Negro | LP701362 | Sí | Curado al azufre |
EPDM | 75 | Amarillo | LP754361 | Sí | |
VMQ | 50 | Azul | JA506376 | Sí | |
VMQ | 50 | Azul | JA506371 | ||
VMQ | 70 | Azul | JA706368 | Sí | Peróxido curado |
VMQ | 75 | Rojo | JA752363 | Sí |
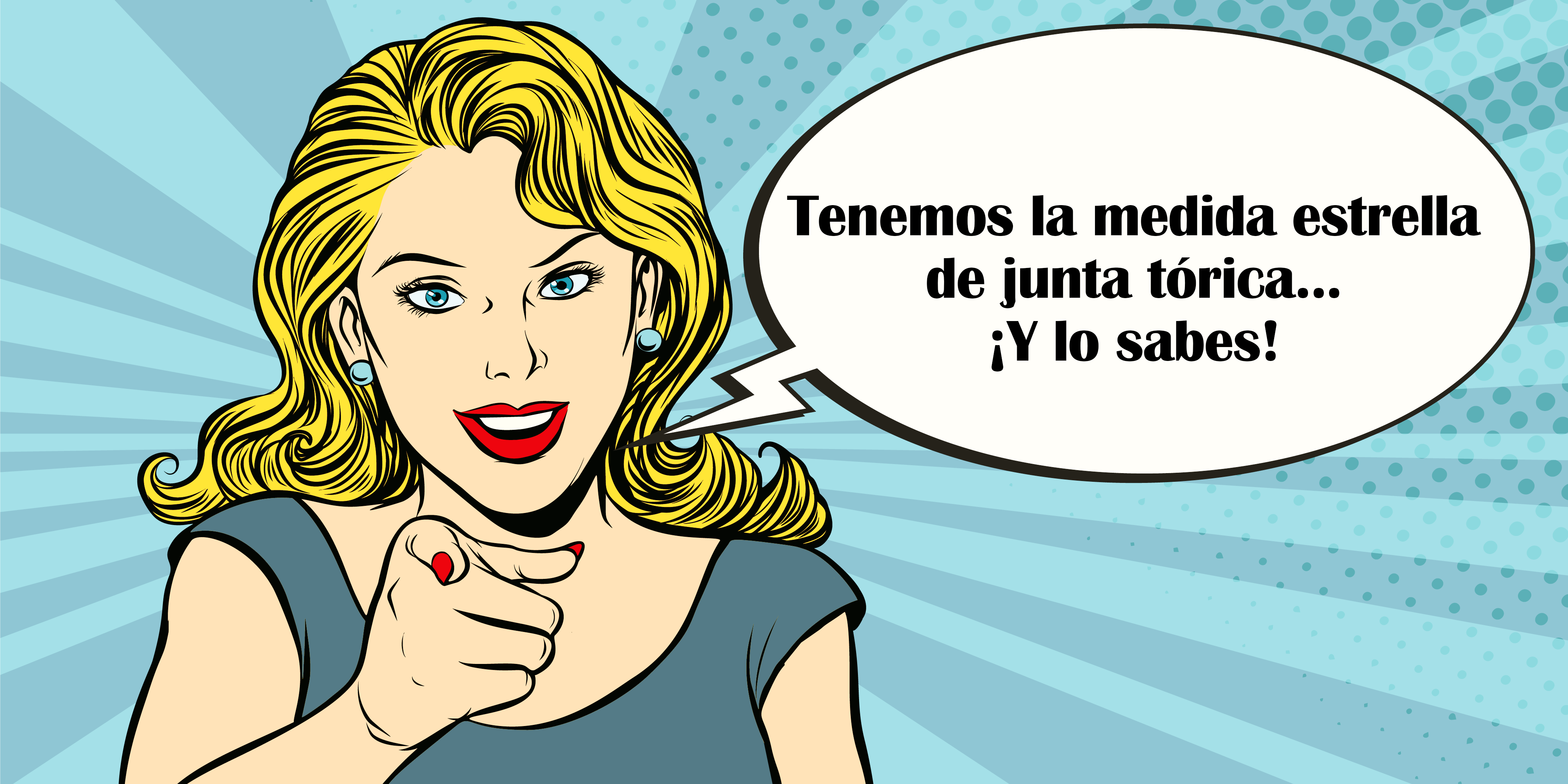
Does the size 4.47 × 1.78 mean anything to you?
You won’t find more materials available anywhere else!
Whereas in the previous post we talked about the importance (or not) of size, this time we are going to talk about the relevance of a specific size. If you are asking yourself why, then just keep reading.
The JIOrings warehouses hold a stock of more than 30 million O-rings of different inside diameters, cross-sections, hardness, materials, approvals, colours… And only the client knows the real working conditions to which the seals will be subjected and the properties that need to be complied with.
Without wishing to be exhaustive, we would like to emphasise the importance of choosing the right o-ring. The use of seals is universal and you will see them in both static and dynamic applications, on the interior and exterior of machinery parts and in a wide range of sectors. Of course, the same seals are not used in the healthcare sector, where O-rings need to be resistant to fluid, inert, and not produce substances or alter the essential characteristics of the product, as the seals used in the hydraulic sector, where resistance to extrusion and oils is more important.
There is a specific size (4.47 x 1.78) that due to its consumption in different sectors (food, pharmaceutical, medicine, biotechnology, chemical, petrochemical, gas, aeronautics, electronics…), we have managed to create a huge stock of different materials and approvals.
Check out our stock of 4.47 x 1.78 O-rings
Reference | Type | Size | Material | Colour | Standard | Homologation |
O0004470178CR7001 | O-Ring | 4.47 x 1.78 | CR70 | Black | (BS008-AN3-2018-103) | |
O0004470178FFKMN894 | O-Ring | 4.47 x 1.78 | FFKM75 (Evolast® N894) | Black | (BS008-AN3-2018-103) | |
O0004470178IB5501 | O-Ring | 4.47 x 1.78 | NBR55 | Black | (BS008-AN3-2018-103) | |
O0004470178IB8001 | O-Ring | 4.47 x 1.78 | NBR80 | Black | (BS008-AN3-2018-103) | |
O0004470178IBM748 | O-Ring | 4.47 x 1.78 | NBR90 | Black | (BS008-AN3-2018-103) | |
O0004470178IBNS7004K | O-Ring | 4.47 x 1.78 | NBR70 | Black | (BS008-AN3-2018-103) | |
O0004470178IBNS8012K | O-Ring | 4.47 x 1.78 | NBR80 | Black | (BS008-AN3-2018-103) | |
O0004470178IBNS9015K | O-Ring | 4.47 x 1.78 | NBR90 (Nipol®) | Black | (BS008-AN3-2018-103) | |
O0004470178JA5002F | O-Ring | 4.47 x 1.78 | VMQ50 | Blue | (BS008-AN3-2018-103) | FDA – Compliant |
O0004470178JA7006F | O-Ring | 4.47 x 1.78 | VMQ70 | Red | (BS008-AN3-2018-103) | FDA – Approved |
O0004470178JA8013F | O-Ring | 4.47 x 1.78 | VMQ80 | White | (BS008-AN3-2018-103) | FDA – Compliant |
O0004470178JAS70R00E | O-Ring | 4.47 x 1.78 | VMQ70 | Red | (BS008-AN3-2018-103) | For gas |
O0004470178LPE70N00C | O-Ring | 4.47 x 1.78 | EPDM70 Peroxide | Black | (BS008-AN3-2018-103) | FDA – Compliant |
O0004470178LPM534 | O-Ring | 4.47 x 1.78 | EPDM70 Peroxide | Black | (BS008-AN3-2018-103) | FDA – Approved for drinking water |
O0004470178OZ7501F | O-Ring | 4.47 x 1.78 | FPM75 | Black | (BS008-AN3-2018-103) | FDA – Approved |
O0004470178OZ819001 | O-Ring | 4.47 x 1.78 | FPM80 | Brown | (BS008-AN3-2018-103) | |
O0004470178OZ910701 | O-Ring | 4.47 x 1.78 | FPM90 | Black | (BS008-AN3-2018-103) | |
O0004470178OZV80V00E | O-Ring | 4.47 x 1.78 | FPM80 | Green | (BS008-AN3-2018-103) | |
O0004470178OZVA7523K | O-Ring | 4.47 x 1.78 | FPM75 (Viton®) | Black | (BS008-AN3-2018-103) | |
O0004470178OZVG70I00 | O-Ring | 4.47 x 1.78 | FPM70 | Green | (BS008-AN3-2018-103) | For gas |
O0004470178TH7003 | O-Ring | 4.47 x 1.78 | HNBR70 | Green | (BS008-AN3-2018-103) | |
O0004470178FE8001 | O-Ring | 4.47 x 1.78 | FEPM80 (Aflas®) | Black | (BS008-AN3-2018-103) | |
O0004470178LP8001PFA | O-Ring | 4.47 x 1.78 | EPDM80 Peroxide | Black | (BS008-AN3-2018-103) | FDA – Approved for drinking water |
O0004470178IB7001F | O-Ring | 4.47 x 1.78 | NBR70 FDA | Black | (BS008-AN3-2018-103) | |
O0004470178FS7002 | O-Ring | 4.47 x 1.78 | FVMQ70 | Blue | (BS008-AN3-2018-103) | |
O0004470178PT17301 | O-Ring | 4.47 x 1.78 | PTFE | White | (BS008-AN3-2018-103) | FDA – Compliant |
O0004470178PU9012 | O-Ring | 4.47 x 1.78 | PU90 | Translucent | (BS008-AN3-2018-103) |
Basic information on the materials used
NBR Acrylonitrile butadiene rubber (NBR) is the most widely used material in O-rings due to its excellent mechanical properties, resistance to abrasion, low permeability to gases and high resistance to mineral oils and greases. [ NBR O-Rings]
EPDM Ethylene Propylene Diene Rubber or EPDM is an elastomer thermopolymer that provides good resistance to abrasion and wear for O-rings. [ EPDM O-Rings]
VMQ The term silicone includes a large group of materials of which VMQ (vinyl-methyl-silicone) is one. Silicone elastomers have may useful properties, the most noteworthy of which are good heat resistance and low-temperature flexibility. There are also highly resistant to ozone and the passage of time, in addition to having good insulating and physiologically neutral properties. [ VMQ O-Rings]
FPM-Viton® O-Rings FPM is a fluoroelastomer obtained from the derivation of synthetic rubber and elastomer fluoropolymer. O-rings manufactured from this material provide greater elasticity and resistance than other types of rubber, in addition to possessing high resistance to highly aggressive fluids, good resistance to deformation, excellent sealing force retention and the original hardness of the design. [ FPM-Viton® O-Rings]
FFKM Evolast® Perfluoroelastomer-made (FFKM Evolast®) O-rings are designed to combine the needs of chemical and thermal resistance provided by the PTFE and the sealing properties typical of elastomers. One of the advantages of seals made with FFKM is the wide range of temperatures they are capable of withstanding. [ FFKM Evolast® O-Rings]
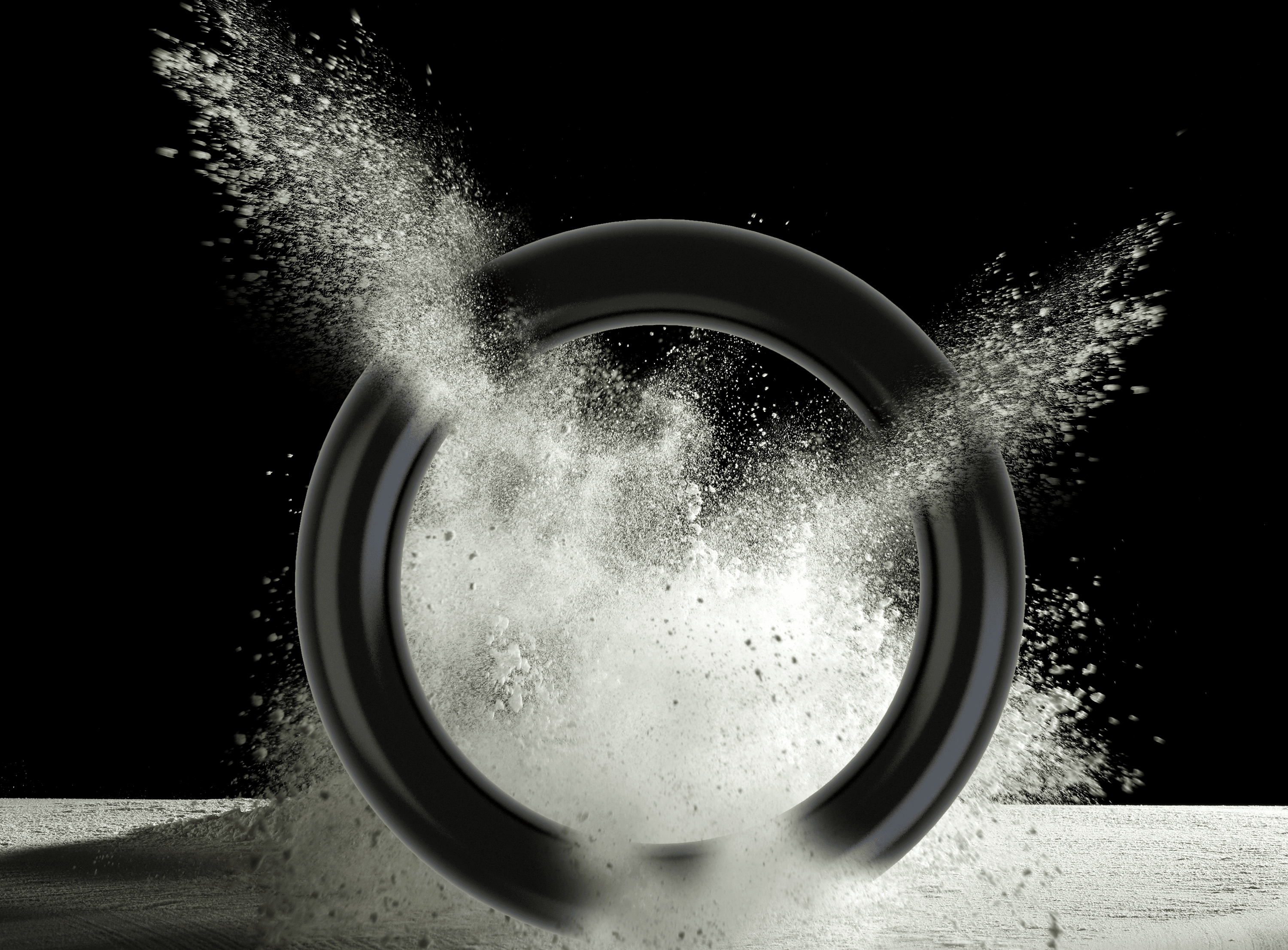
Do you know which specialised treatments apply to O-Rings?
Treatments that improve the performance of O-Rings
Sometimes standard elastomer O-Rings need to be treated with specialised surface treatments. By doing this, the equipment’s performance, assembly and installation is improved.
At JIOrings we can treat the O-Rings surface with specialised processes such as cleaning, chemical immersion or coating, with the aim of reducing friction and adhesion, to achieve a permanent lubricating effect or to facilitate the installation of the gaskets.
These treatments are usually done for large quantities or batches anyway, in case you need this type of treatment, we recommend that you contact us so we can analyse your needs and offer you the appropriate solution. These are the different treatments or surface coatings that we offer:
• PTFE
• Coloured PTFE
• Siliconized
• Talc
• Micro Talc
• Molykote
• Graffiti
• Chloride
• Rough
*Download of the technical specifications for each treatment, is subject to the purchase of gaskets treated to any of the aforementioned coatings.
PTFE
PTFE (Polytetrafluoroethylene coating), also known as TEFLON® (trademark of Chemours), is a coating based on fluoropolymers that provides high anti-adhesion to gaskets.
PTFE is a material suitable for contact with food (FDA), so it has many industrial applications such as the food, beverage, chemical and textile sectors etc… The process for coating gaskets with Teflon® PTFE consists of four different parts:
• Degreasing – Consists of eliminating any organic or inorganic residue that the pieces may have. For this, degreaser is applied to the gaskets.
• Sandblasting – Or preparing the surface to be coated to guarantee maximum adhesion of the Teflon® by blasting with aluminium oxide.
• Application – This is done with liquid spray guns, electrostatically, HVLP or with powder guns. This process may consist of several layers of product, depending on the purpose of the coating.
• Curing – For Teflon® to maintain its properties, the coating must be polymerised. Which means heating the gaskets to 360°C and maintaining this for 10 minutes.
Siliconised
The silicone or siliconised coating provides the gaskets with greater anti-adhesion, waterproofing and mechanical resistance. In addition, silicone gaskets also have better sealing and thermal insulation. A silicone gasket has the following advantages:
• Better thermal resistance.
• Good inflammability properties.
• Excellent impermeability (even in hostile conditions: outdoors, water, steam, smoke and combustible gases).
• Good flexibility.
• Can be cleaned easily.
• Increased durability.
MOLYKOTE
Molykote is Dow Corning’s commercial name for their specialised lubricants. This lubricant was developed to solve industrial lubrication problems, and in turn to reduce friction and wear.
By treating the O-Rings with Molykote, which incorporates molybdenum disulphide (MoS2) into the lubricant, it is possible to create a final product capable of withstanding high loads, high and low working temperatures, dirt and dust, aggressive chemical environments and extreme speeds.
The MoS2 is incorporated into the elastomer in the form of a dry lubricating film dispersed over the sealing surface. This produces a mechanical interlacing, which in the long term, reduces the friction and wear caused by dynamic stresses. The main advantages of this type of treatment are:
• Improved separation in automatic assembly.
• Reduced friction and dynamic tension.
• Pollution containment.
• Protection against corrosion.
• Dispelled heat.
• Power transmission.
• This process is suitable for all types of elastomers.
When this static lubricant is applied to O-Rings, it allows for their use in advanced applications that require high electrical conduction, heat transfer, vacuum sealing and/or stability of a join.
TALC
It is often necessary to improve the coefficient of the O-Rings friction, since they have rough and adherent surfaces. In these cases, surface treatments such as talc can be applied. Thanks to this method, a reduction in friction can be achieved, both to facilitate assembly and to prolong service life.
Talc treatment, consists of applying it to the gaskets in a drum as a coating of disseminated dust. In this case, no interlacing occurs with the surface of the elastomer.
The talcum powder particles create an impermeable barrier that reduces the penetration of air and liquids into the gaskets. The more laminar the talc, the greater the barrier effect it will have. These are the main advantages of a talc-based treatment:
• Disseminated powder coating.
• It prevents the components from sticking once packaged.
• It is not suitable for dynamic applications.
• This process is suitable for all types of elastomers.
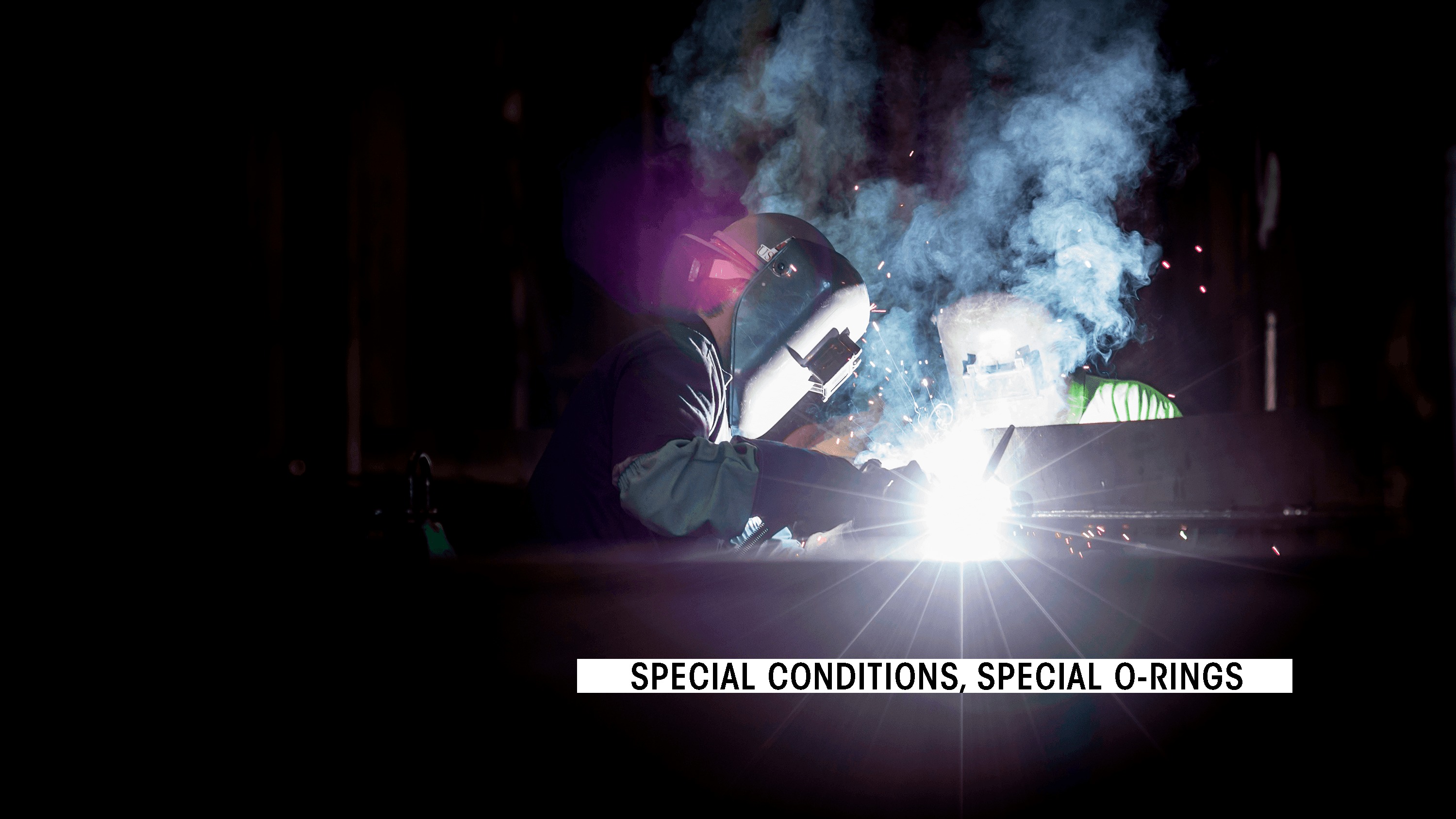
Mixtures with specialised homolagations
Do you need seals with specialised homologations?
On more than one occasion we have commented on the importance of the choice of O-Ring seal. O-Rings are suitable for both dynamic and static applications but their success will depend on the properties of the gasket and the design of the housing.
The correct measurement, material, hardness, the temperature it will be subjected to, and the conditions in which it will be sealing. All these parameters have to be taken into account when selecting the gasket. Don’t forget that the O-Ring must comply with the special homologations that certify its suitability to come into contact with drinking water, food, beverages, medicines, fire, gas etc.
JIOrings O-Rings application is wide and varied, and is commonly used in food, health, automotive, aeronautics and oil sectors etc. but these gaskets are also present in many home appliances available at our fingertips.
Whatever the final destination, our goal is that the seals treatments always comply with health requirements, drinkability and safety required in each case by each client. That is why we have been working for years to have seals materials certified by entities and independent laboratories.
In this table you can check which mixtures comply with international homologations, and the origin of the country that issues them.
Homologations and Certifications
APPROVALS | COUNTRY | NBR | EPDM peroxide | EPDM | HNBR | FKM | VMQ |
3a SANITARY | USA | EPDM70 | |||||
BS6920 WRAS |
England | NBR70 | EPDM70 | FKM70 green | |||
CLP ACS COMPLIANCE |
France | NBR70 | EPDM70 | ||||
DM174 | Italy | NBR70 | |||||
EN549 DVGW |
Germany | NBR60 NBR50 |
VMQ80 | ||||
EN681 DVGW |
Germany | EPDM70 | |||||
EN682 | Germany | NBR70 | |||||
EN71-3 | Italy | VMQ70 red A1:2014 migration test |
|||||
FDA | USA | NBR55 NBR70 NBR80 NBR90 |
EPDM70 EPDM80 |
EPDM70 | HNBR70 HNBR70 green |
FKM70 FKM70 green |
VMQ 40 Sh a 80 Sh various colors |
KIWA BRL-K17504 |
Netherlands | EPDM70 | |||||
NSF61 | USA | EPDM70 | |||||
ÖNORM B 5014-1:2016 |
Austria | EPDM70 | |||||
UBA | Germany | NBR 70 | EPDM70 | ||||
UL778 | USA | NBR70 | EPDM70 | ||||
USP 32 <87> | USA | EPDM70 | |||||
USP VI <88> | USA | EPDM70 | |||||
W270 TZW |
Germany | NBR70 | EPDM70 | ||||
W534 DVGW |
Germany | EPDM70 | |||||
CE1935/2004 | Europe | NBR70 | EPDM70 | VMQ | |||
GSMark | Germany | FKM except black |
VMQ |
Approvals and certifications
DRINKING WATER | GAS | FOOD/PHARMACY |
• ACS: Declaración de Conformidad Sanitaria (ACS-CLP) • KIWA • KTW: Kunststoffe und Trinkwasser • NSF: National Sanitation Foundation • WRC: Water Research Council • ÖNORM: Austrian Standards Institute • DVGW: Deutsche Vereiningung des Gas und Wasserfaches |
• DVGW: Deutsche Vereinigung des Gas und Wasserfaches | • USP: United States Pharmacopoeia • FDA: Food and Drug Administration • BfR: Bundesinstitut für Risikobewertung • ADI: Ingredient Derived from Animals • 3 A: 3 A Sanitary Standard |